tomsworkbench.com/2009/11/02/stuff-ive-built-my-krenov-style-plane/
This project started with a meeting with Ron Hock.

http://www.hocktools.com/FAQ.htm
http://www.hocktools.com/A2.htm
These blades were developed in collaboration with the faculty and staff at James Krenov's Fine-Woodworking studio here in Fort Bragg. 3/16" thick, they won't deflect or chatter under the toughest use. Designed specifically for the finely-tuned handmade wooden plane, these irons are un-beatable. Bevel is 30°. They come complete with chip-breaker and assembly screw. High carbon steel.
At the 2009 Woodworking in America conference, Ron was there as a featured vendor. At his table was a choice selection of his plane irons. I told Ron I was considering purchasing a smoothing plane with a little more oomph than my Stanley No. 4. Ron was quick to recommend that perhaps the best solution might be to build my own.
That’s when I laid out the money for a 2″ Hock iron and stared looking into plans for building a Krenov-inspired model. With the plans from Popular Mechanics and some help from Bell Forest Products, I soon had a block of bubinga and instructions to work from.
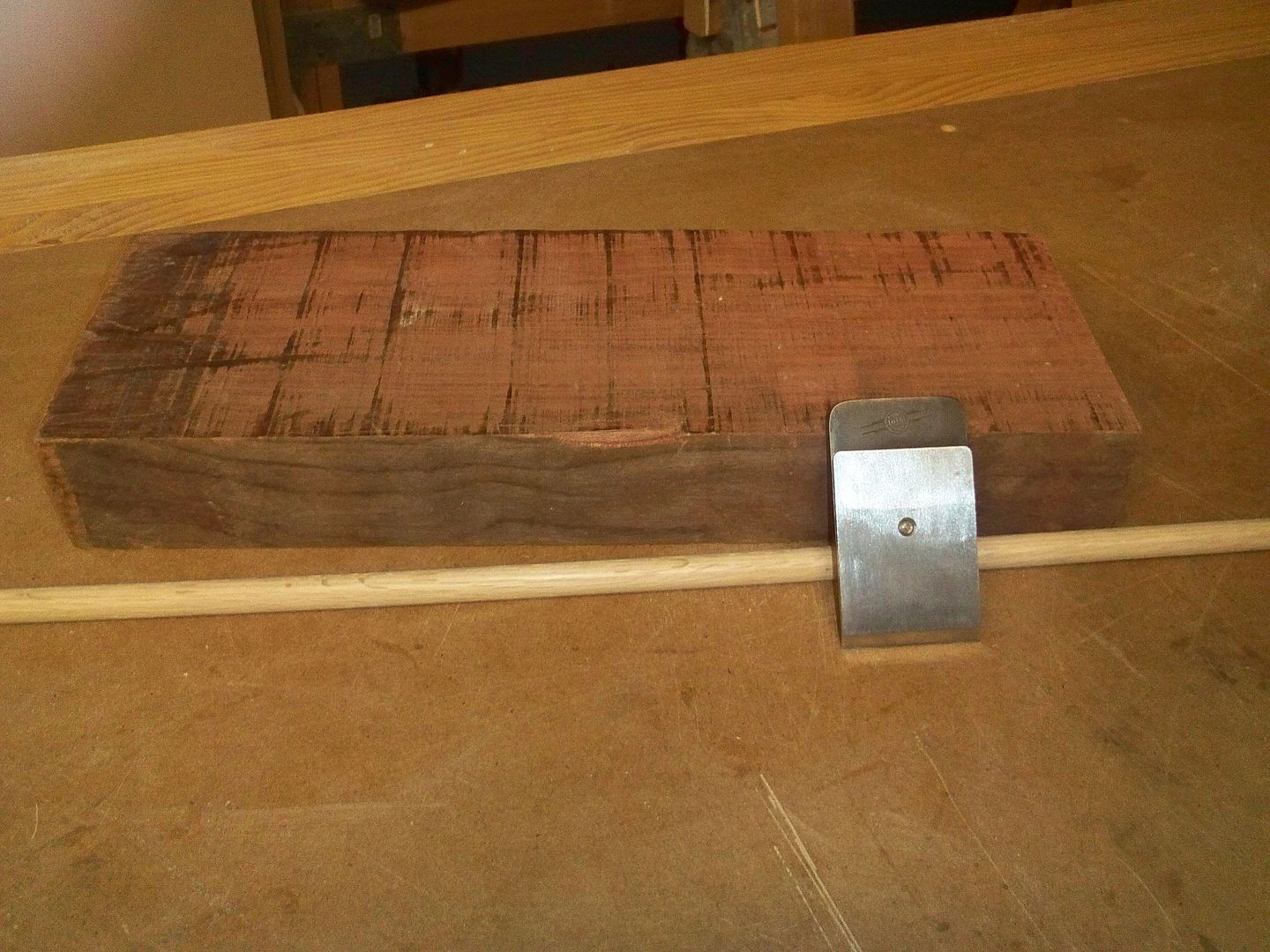
Now, I’ll tell you I was terrified to start. I mean, what if I had just wasted all that money on the iron and the wood? A few e-mails back to Ron brought more encouragement. “Tom, look at it this way,” Ron wrote, “If you mess up badly, you are only out about a board foot or two of wood. You can start over and do it again.”
The first part was easy… I had to edge and face joint the board to make everything nice and smooth. Soon, the rough surface gave way to the lovely shade I had come to expect from bubinga. Dead flat and four square.
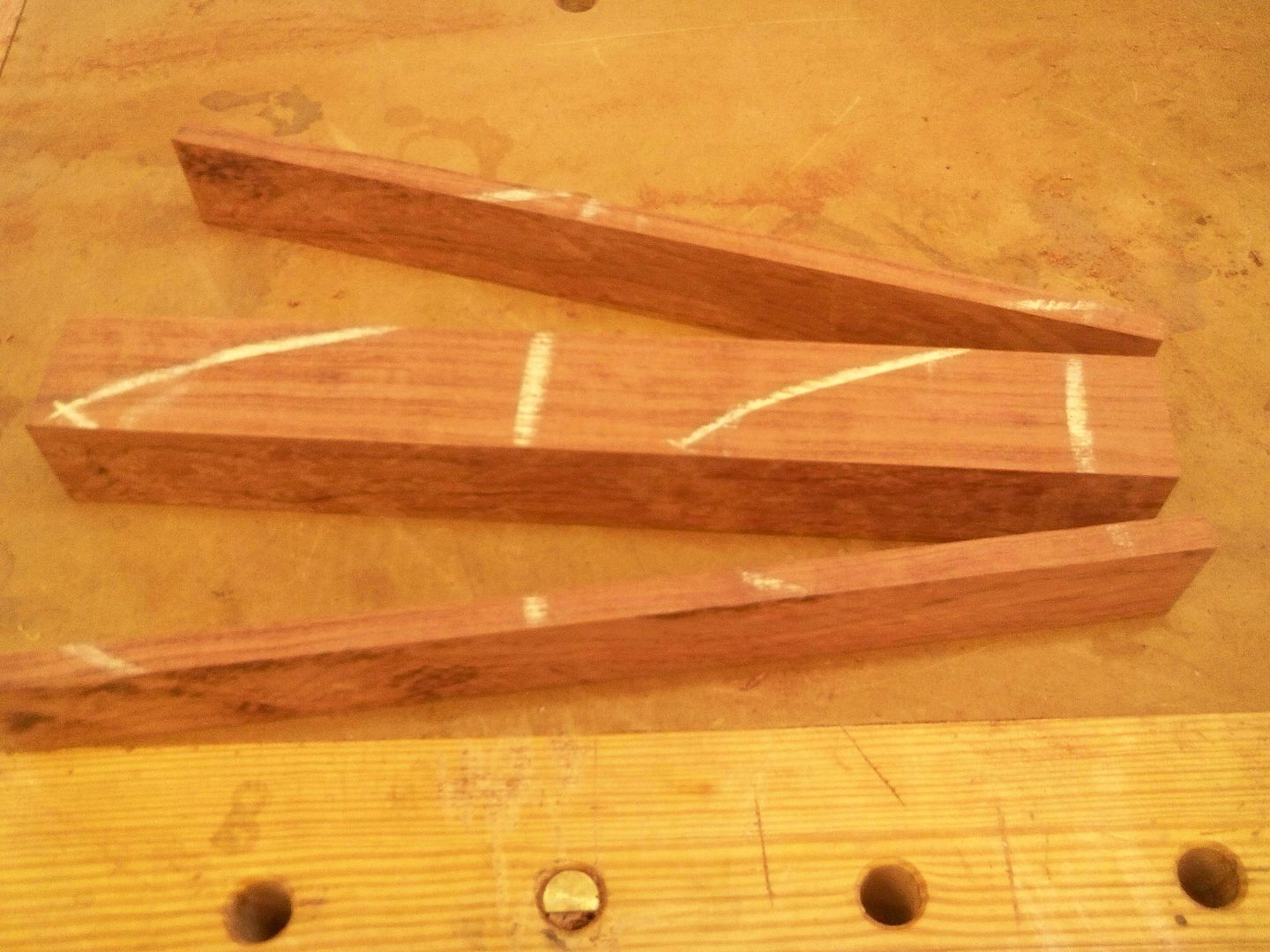
The next step was easy as well…. Rip one cheek at one half inch, then the plane body at 2 1/16″ to accommodate the iron, then the other cheek. I used a cabinetmaker’s triangle to ensure everything would stay oriented.
The directions then called for me to cut the plane body block at 45 degrees. At the table saw, this took only seconds, and the results were stunning. Dead flat on the face and a true 90 degrees to the edge.
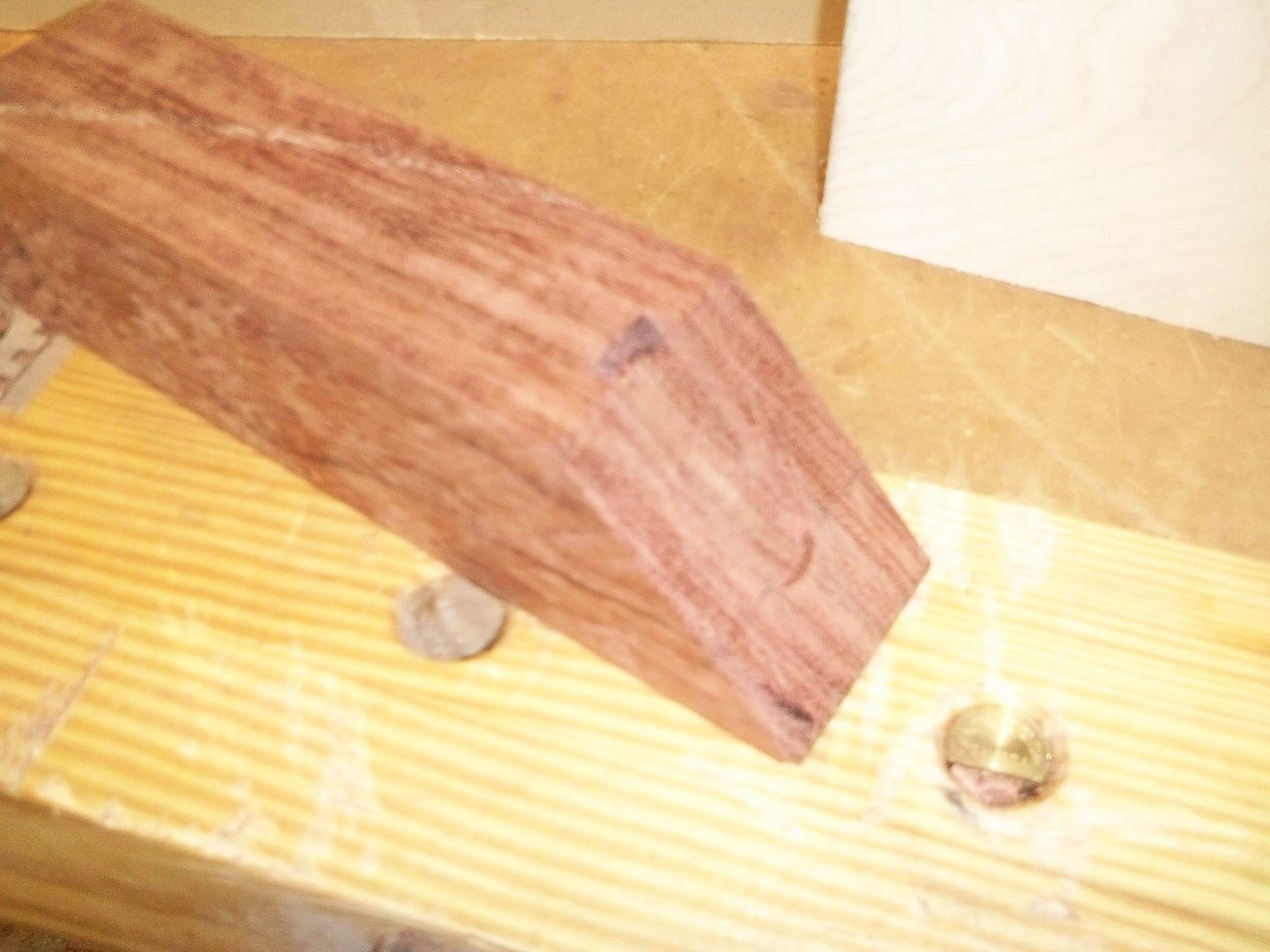
I put a 3/4″ router bit in my table mounted router in order to make a relief groove to accept the screw that holds the iron and the chipbreaker together. Ron’s irons have a pretty beefy screw, but it was easy to center the bit on the block and make the cut.
By simply flipping the other body blank upside down, I formed the gullet of the plane. The instructions said to file a flat spot at the miter point of the block that holds the iron, then space the two pieces 3/8″ apart to allow clearance for the iron. I clamped both blocks to the cheeks and carefully marked where they had to be when I glued the plane together.
I took both cheeks and stacked them together, then drilled a 1/2″ hole through the cheeks at a mark in the gullet to receive the cross pin. The plans called for me to create a complicated tennoned rotating pin to hold the wedge in place, but Ron advised me to just go with a fixed pin – it would save time and work just as well. I took a length of 1/2″ oak dowel I had the shop and cut it a little longer than the plan called for so I would have excess I could trim.
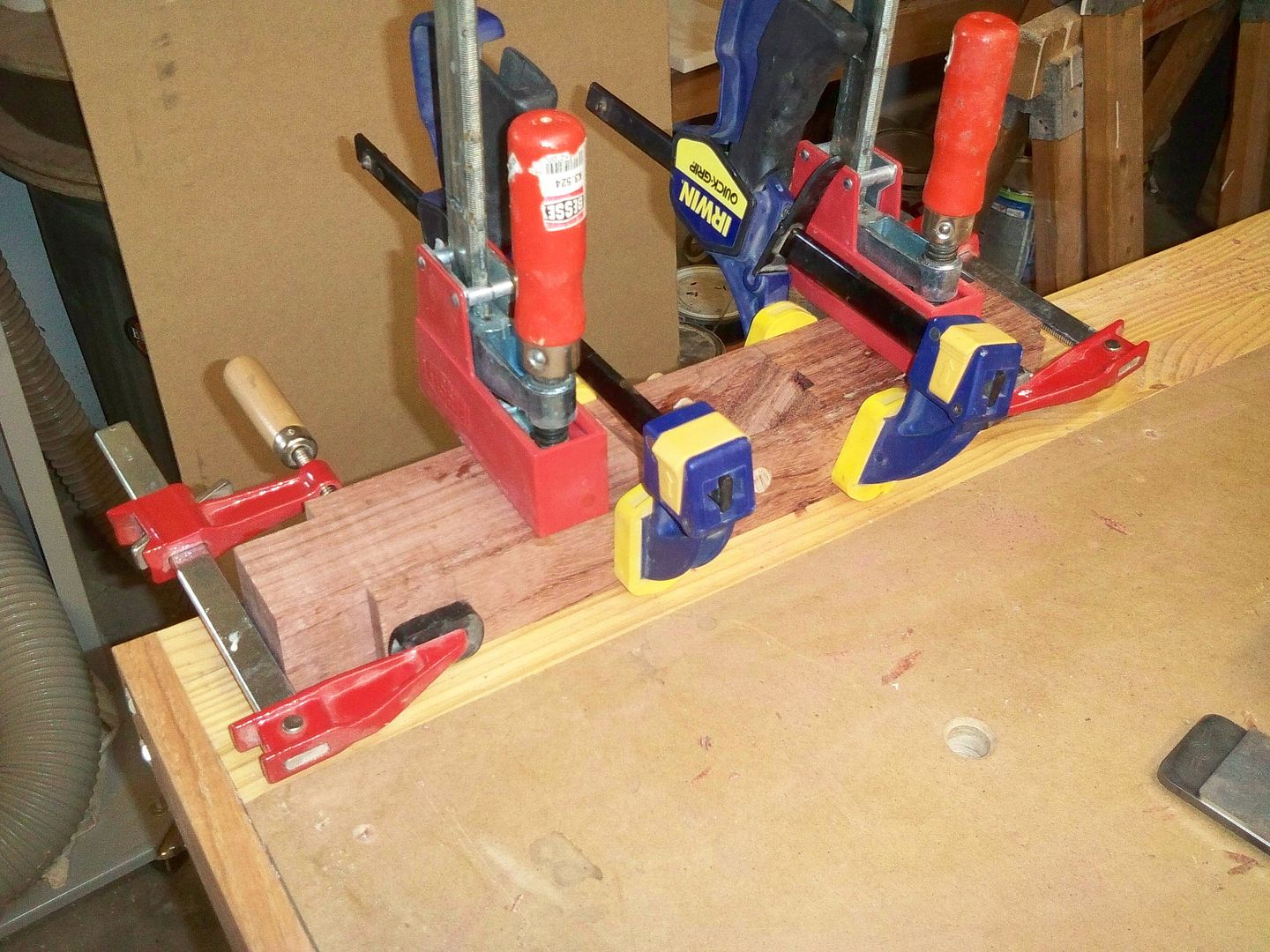
Then came the glue up. I lay one cheek flat on my bench and put glue on it – staying clear of the gullet area – then put the two body pieces in the places I had marked earlier. Then, I put glue on the tops of the body halves and one end of the oak pin. I slipped the oak pin into one of the cheeks and then put the other cheek on the top side of the assembly.
The next step I found to be critical. Not only did I clamp the assembly together across the width, I also clamped it down to the bench to ensure things would line up. Once I was satisfied, I went on to build the wedge.
After cutting an appropriate piece from the remaining bubinga, I put it into the vise and started to shape it with hand tools. I didn’t want to overshoot my thickness, so I worked carefully with a few rasps and a block plane to bring things down gradually. Before long, I had the wedge to the right thickness and I was ready to work.
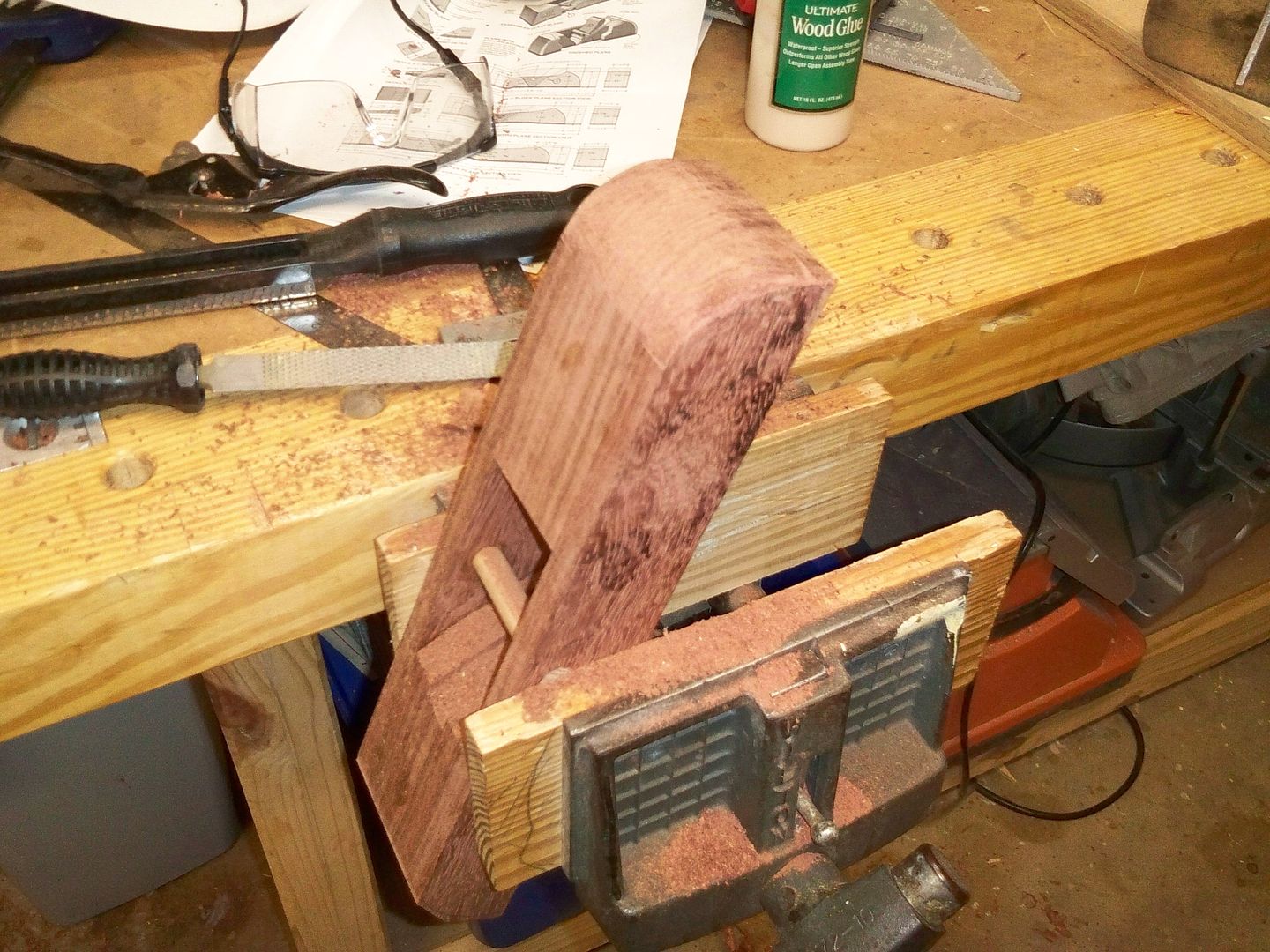
I took the plane out of the clamps, and started to shape it. I cut the plane to length and then worked on rounding over the front and back edges. I used the band saw, rasps and a belt sander – bubinga is tough stuff. Once I was happy, I flipped the plane over and ran the sander over the sole. I wanted it dead flat, so I kept checking with a straight edge. Once I had it nice and flat, I finished it off with a scraper to get the surface nice and smooth.
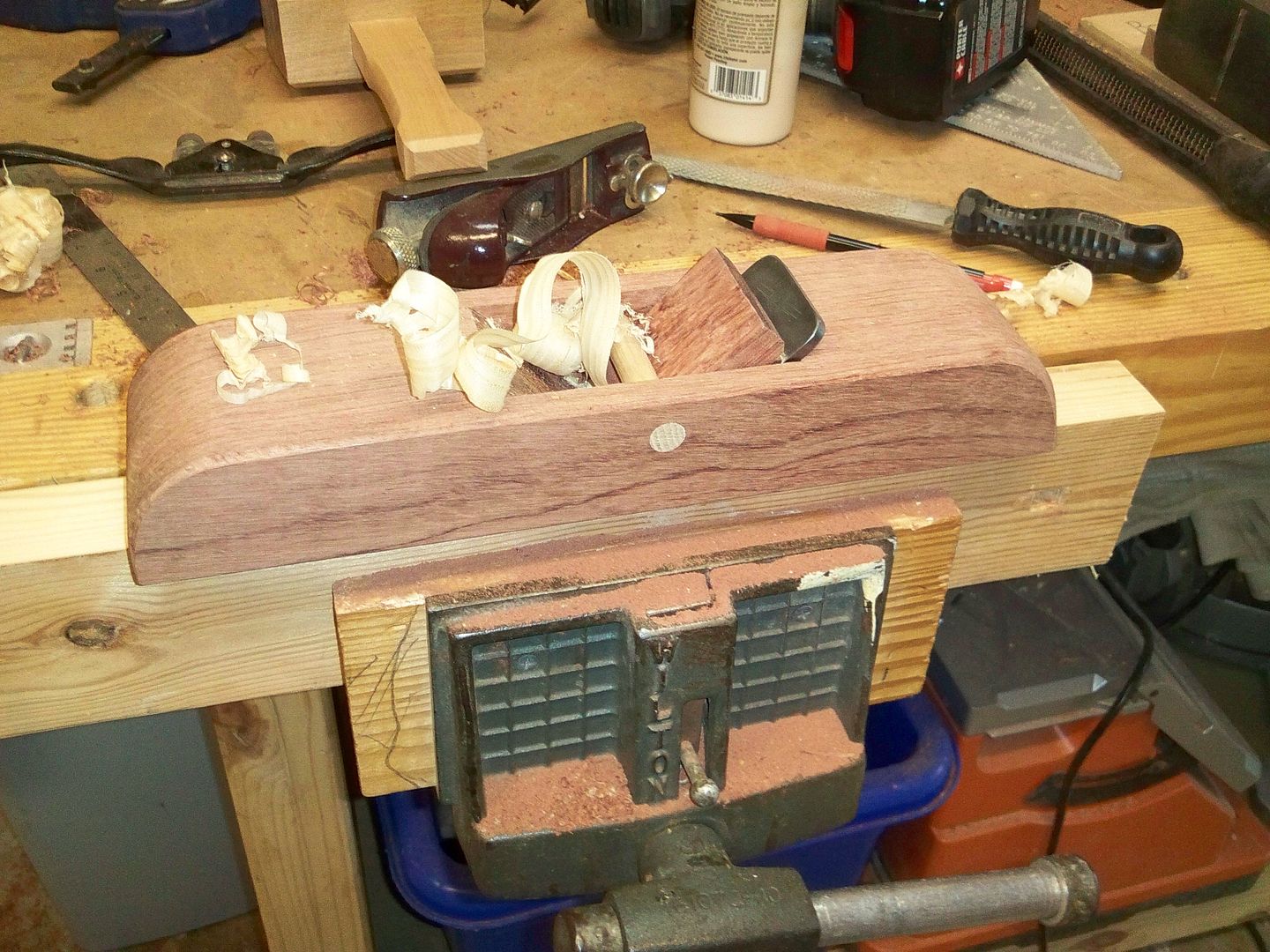
The came the moment of truth. Would it even cut? I put the iron in and tapped the wedge into place. It took some fussing at first, but once I got the iron where I wanted it, it cut beautifully! I do need to get my hands on a plane hammer – my carpenter’s mallet isn’t going to cut it adjusting the iron. But, other than that, the plane works great.
The time invested was so small… one Sunday afternoon. If I hadn’t stopped to watch football and tend to the laundry, it might have taken me about two hours. The results, however, were pretty spectacular.
Not a bad way to spend a weekend in the shop!
=================================
No comments:
Post a Comment