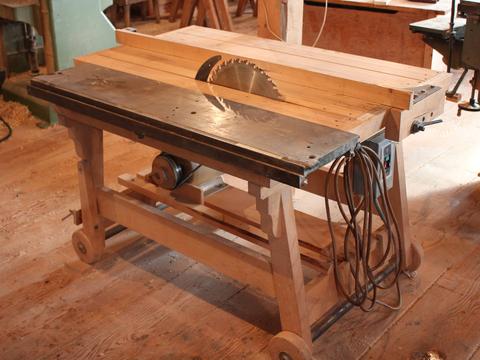
Back around 1993, my dad built a wooden table saw to use as a second table saw in his workshop
The key parts of this saw were a function of opportunity. When he originally bought his Felder KFS 36 in 1986, it came with an arbor with a slight wobble to it and a sliding table that wore out prematurely. Felder sent a technician from Austria to replace those parts, but dad kept the old parts, which he eventually used to build another table saw.
The problem with the arbor had been a dent in the flange, which we straightened out with a hand file before the technician even came. But the sliding table had ball bearing balls that ran directly in grooves in the cast iron. These wore into the cast iron relatively quickly, so the table developed some play. Basically, a defective design. The replacement table was a different design. I should add that the Felder KFS 36 was a brand new model at the time, but has long ago been replaced with newer models.
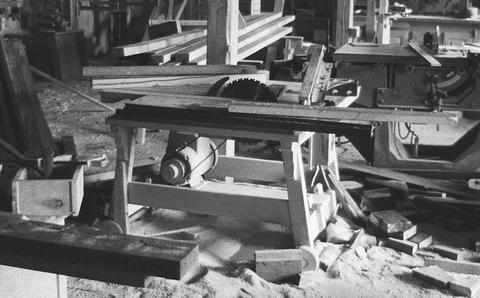
There was no way to catch the dust coming from this saw, but my dad never believed in dust extraction, so that wasn't an issue.
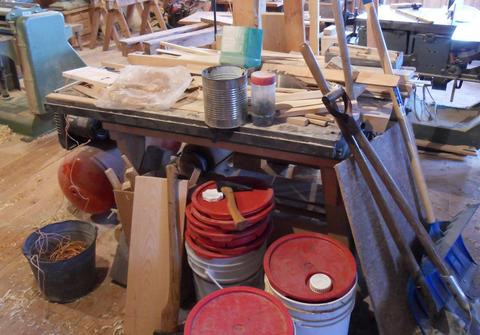
While it's handy to have a spare saw to make some cuts while the other table saw is set up for something else, the problem with this saw was that it was never a saw for making finishing cuts. One usually doesn't have any special cuts set up while initially sizing the lumber for a project, so it was just as handy to use the main table saw for that.
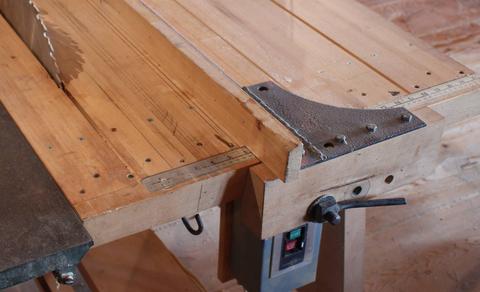
An aluminium ruler embedded in the table serves as a scale for setting the rip fence.
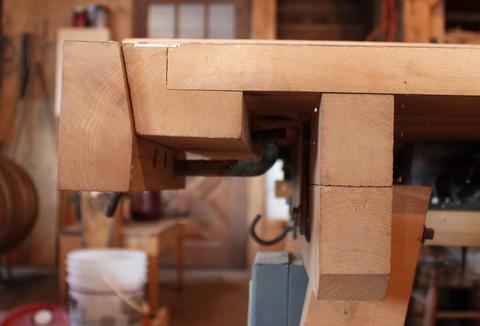
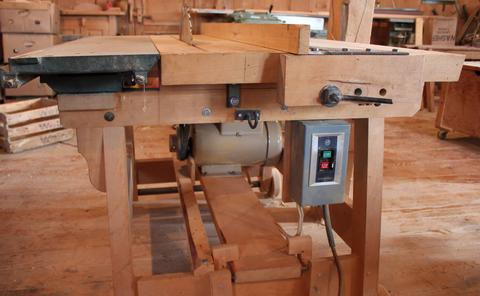
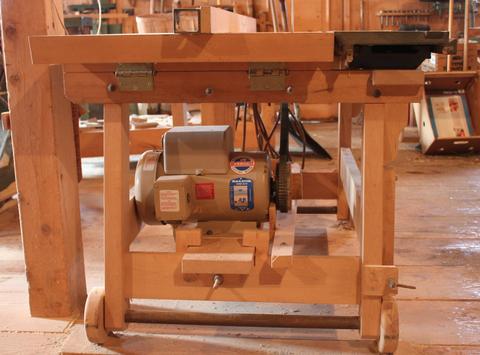
You can also see the green hinges under the table (used hinges, of course). These are for a simple "height adjustment".
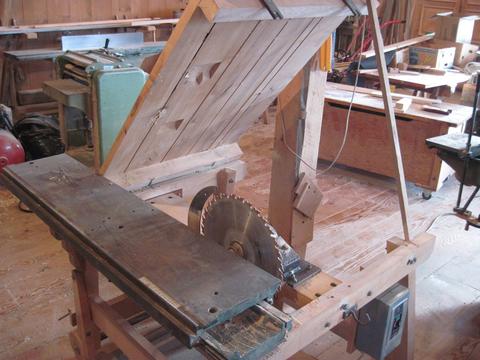
The blade is completely fixed in place, no tilting arbor.
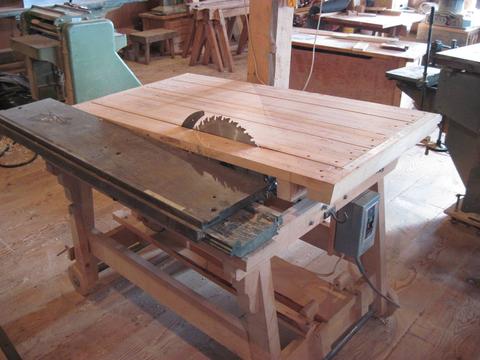
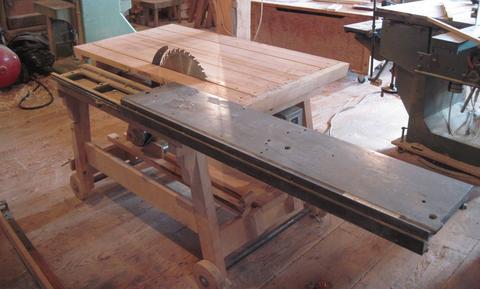
It was exactly the same size sliding table as the new one on the Felder KFS 36, so my dad could just take the crosscut fence and table extensions off the Felder and attach them to this one for cross cuts.
The sliding table does have a fair bit of play in it in the middle of its travel, but this saw wasn't meant to be super precise, so it didn't matter that much.
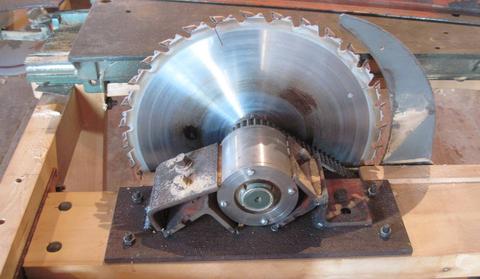
Various bits of angle iron welded to a steel plate make up the mount for the arbor.
On Felder table saws, the drive belt is just behind the arbor flange. The motor is mounted very close to the arbor, behind the blade, so that the shaft of the motor is actually behind the blade. This makes for a very compact drive unit for the saw.
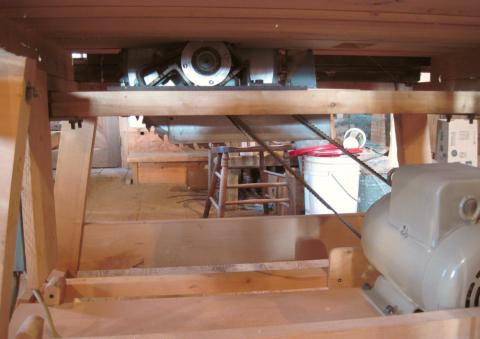
The belt is a worn out timing belt, flipped inside out so that the smooth side is against the crowned pulleys.
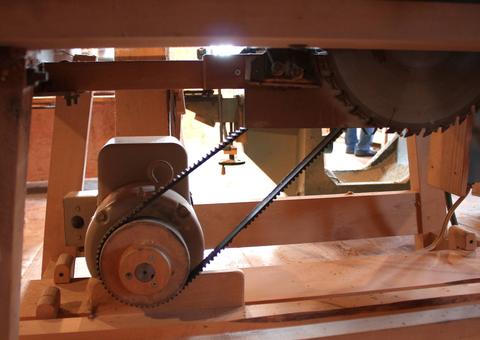
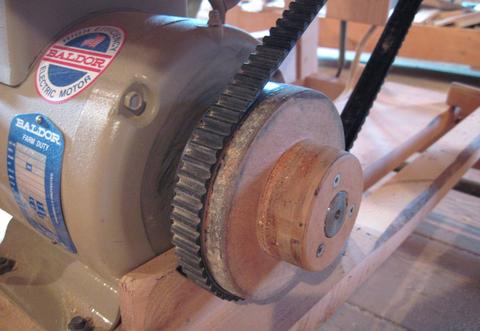
The motor pulley doesn't have much of a crown to it, and you can see by the scuff marks on the motor housing that it had slipped off at some point. A piece of wood between the pulley and motor now prevents the belt from coming off this way.
A problem with flat belts is that they need a lot of tension and quite a bit of precision to track well.
Also, the motor, with its very high starting torque, always causes the belt to slip a little before the blade comes up to speed.
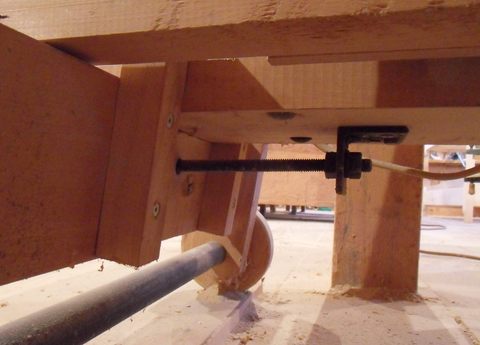
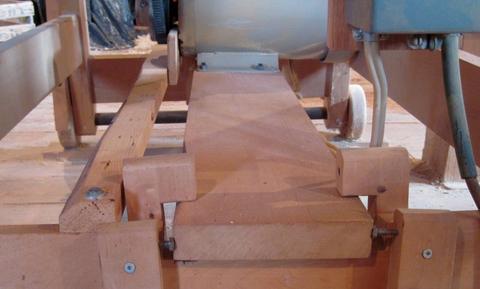
Most machines that use flat belts don't have a tracking adjustment. They are made precisely enough to make that unnecessary. But this is a wooden machine using a worn out timing belt as a drive belt, so having a facility to adjust belt tracking helps.
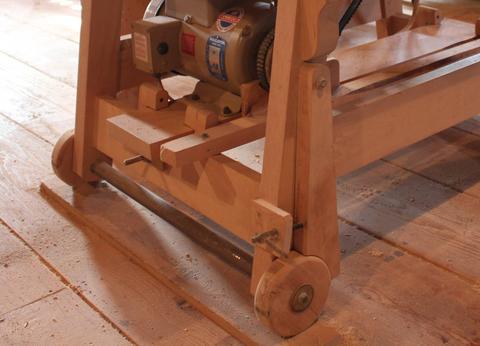
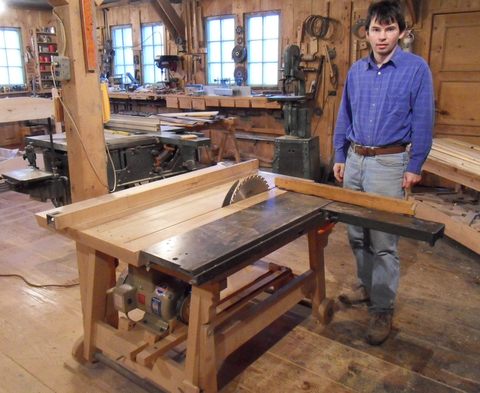
I can't say this saw was a tremendously successful project, seeing that my dad didn't end up using it anymore after a few years. But it's interesting to see what sort of challenges he faced and how he solved them.
The biggest downside I see with this saw is that it doesn't have a way to lower the blade. With the blade sticking 11 cm (4 3/8") up from the table, it's not really a saw that you want to use for anything but the largest pieces of wood.
....reminds me of my dad....always making things to make other things with, out of whatever was on hand.
ReplyDelete