![]() |
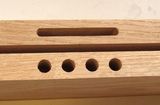
dowel joints revisited
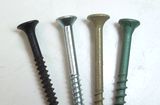
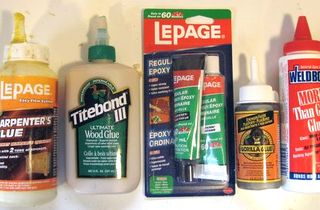
![]() |
Joint strength tests Testing different types of joints |
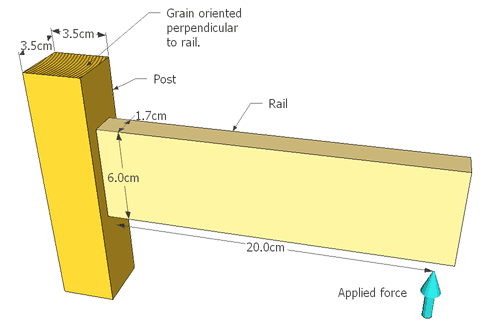
Making joints to test
I decided to standardize the size of my joints to be a 6 x 1.7 cm rail attached to a post 3.5 x 3.5 cm in size. This is close to the size of joint one might use putting together a chair or a stool. It's that sort of joint that gets stressed a lot - so much so that most store-bought wooden chairs will come apart at the joints eventually. I used yellow carpenters glue for all of my tests. For the wood, I used spruce and then retested with maple.
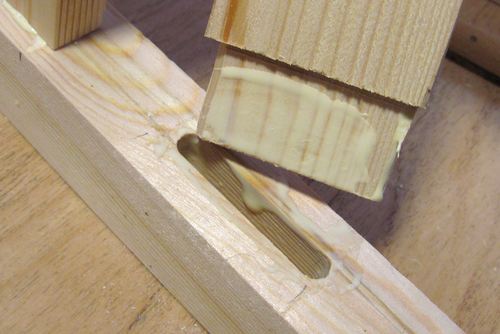
I made a number of mortise and tenon joints, ranging from tight enough that I had to drive it in with a hammer, to some being loose by a few thou, so that the dry fitted joint would still have a tiny bit of play. More about mortise and tenon joint fit and accuracy
[...]
Retesting with maple
I tested two dowel joints with maple. These failed at 230 and 245 pounds. For the mortise and tenon joint in maple, I tested just two joints, which failed at 300 and 270 pounds.
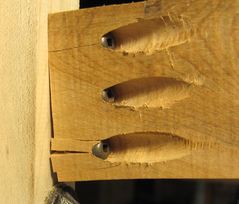
I used 2" #8 screws for the pocket hole joint in maple. The joint failed at 220 pounds, with the pocket holes splitting apart.
The joint with the 3 1/2" screws screwed through the post and into the end grain held up to 160 pounds before the screw heads got pulled into the post. After I put washers behind the screw heads, I was able to load the joint to 300 pounds. At 300 pounds, the joint hadn't 'failed' yet, but it had deflected so far that I considered it pointless to go any further. Even with the extra contact area provided by the washers, the screw heads and washers were just pulling further and further into the maple. The washers also got seriously bent out of shape.
The trouble with screw joints
Overall, all the screwed joints had an unacceptable amount of opening up of the joint before they actually let go. From a furniture building perspective, having a joint open up by a few degrees is unacceptable, so the ultimate strength where the screwed-together joint comes apart really isn't a useful measure in terms of making furniture. That said, the amount of yielding before failure of a screw joint does give it a certain amount of toughness. Failure is gradual, and it takes a lot of energy to get a joint to let go. This means whatever you fasten with screws takes a lot of beating before it fully comes apart. This property is useful if you are building sawhorses, scaffolding, or packing crates. But for furniture making, it doesn't help much. So my conclusion is that for furniture applications where strength is critical, screw joints should be avoided. That said, it's fine to use screws to attach a panel to the back of a dresser or bottom of a box, but you shouldn't rely on screws to hold a chair frame together. If you do use screw joints, I think it's best not to cover the heads, so that if the joint does open up a little, you can at least re-tighten the screws.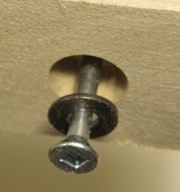
The screws held surprisingly well in the end grain. I also experimented with drilling a slightly larger hole for the screw, and filling the hole in the end grain with glue before inserting the screw. This did improve the holding power even more, yet the screw could still be unscrewed. So that may be an effective technique to repair furniture where the screws have pulled out of the wood.
Force of failure in pounds, applied at 20 cm 1 pound = 0.45 kg = 4.4 Newtons | ||
---|---|---|
Joint type | Spruce | Maple |
Mortise and tenon | 170,175,140,180,185,190 | 300, 270 |
Dowel | 120,140,145 | 230, 245 |
Pocket hole * | 115,110,140 | 220 |
End grain screw * | 85 | 160 |
End grain screw + washers * | 210 | 300 |
* All screw joints deflected to such a large extent before failure that the ultimate failure strength is useless as far as furniture making is concerned.
For reference, I also tested the hardness of the wood I used, using my screwdriver drop hardness test method. My spruce samples divoted by .115" on average, which made it slightly softer than many of the spruce samples in my hardness table. All my spruce is selected for being heavy, so I'm pretty sure the spruce I was using was still slightly harder than the average piece. My hardwood samples tested with divot depths of .035" to .043", which puts it in the middle of the range for the hardwoods.
Further observations
- In my tests, mortise and tenon joints outperformed dowel joints by an average of 25%. This is actually impressive performance for the dowel joints. The outside two dowels were only 47.6 mm apart at the furthest edges, whereas my tenons were 56 mm wide - nearly the width of the stock. I couldn't put the dowels all the way out to the edge of the rail because they still needed wood around them to glue into. The dowels also only protruded 25 mm into the post (half of the length of the pre-cut 2" dowels), and the taper at the end of the dowels also shortened their effective glue area by another millimeter or two. If I had restricted my tenons to the geometry I was forced to with the dowels, I'm pretty sure they would have lost the advantage. That all said, the tenon joints were faster to make and glue up.
- In one of my spruce mortise and tenon joints, I had the growth rings parallel to the tenon. This joint failed by the wood in the post shearing along the growth rings, and failed significantly sooner than expected. So for strength it's probably best to orient the wood so that your tenons cross as many growth rings as possible. I excluded this one sample from my results.
- The first maple mortise and tenon joints that I tested failed much sooner than expected. On close examination, I did not see the usual transfer of fibers from one part to the other. The glue, not the wood had failed. Apparently, for that joint, 36 hours had not been enough to let the glue fully dry. I excluded that sample and waited another 24 hours before testing the remaining hardwood joints.
- The hardwood joints did not show any noticeable deflection or strain on the joint right up to the point of failure. Spruce showed more deflection. The screw joints all caused the joint to open up to an unacceptable degree long before they actually let go.
- A big long screw holds surprisingly well in the wood's end grain. I drilled the pilot holes quite small, so all my rails were in danger of splitting when I put the screw in the end grain. However, another quick test I did was to drill the hole larger, fill it with glue, and then put the screw in. This arrangement held very well, and the screw could still be unscrewed and re-screwed.
No comments:
Post a Comment